Interview: Plastic that doesn’t end up in our oceans
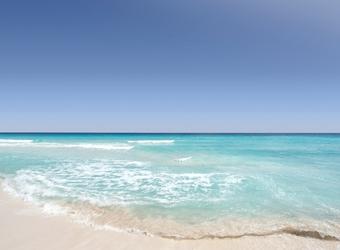
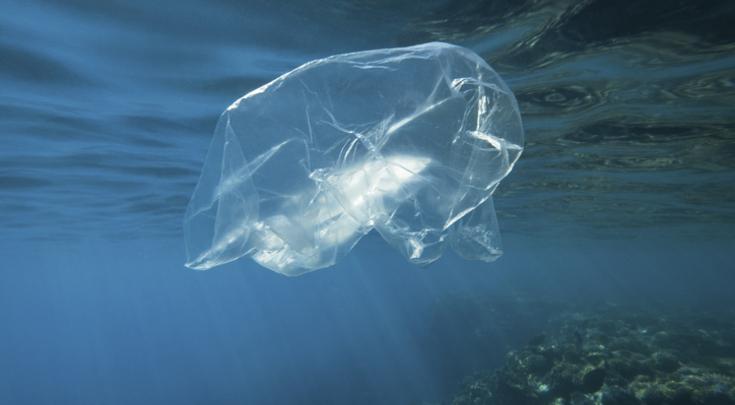
Sustainability in developing plastic profiles is not an end in itself – it needs to be economically viable. To ensure this viability for our customers, development engineers like Dirk Moses are continually working on new plastic solutions to balance technical requirements with sustainability.
In this interview, he offers an insight into his work and the importance of sustainability.
Some people think of engineering plastics first and foremost in terms of their negative environmental impact, followed only then by their advantages over other materials. What would you say to that?
Actually, when people think of plastics, the first thing they think of is plastic bags, microplastics and other plastic waste polluting our oceans. But those are not the kind of plastic products we manufacture here at Technoform. If used correctly and developed sensibly, plastics are even more sustainable that other materials, like metal, for example. One of the reasons for this is that plastics are extremely durable. For example, a plastic container for chemicals under the influence of acids is much more resistant and durable than comparable containers made of metal. In addition, manufacturing processes for aluminium and steel are very energy-intensive compared to plastic.
We strive to completely recycle our plastic products at the end of their life cycle. This works rather well with thermoplastics if we produce profiles using the same mix of materials over several product generations. The used plastic is melted back down and re-processed. Processed thermoplastics’ long service life and optimal recyclability make our plastic profiles highly sustainable products. As I said, these products are not comparable to plastic packaging materials, which, unfortunately, have become a major problem for the environment.
What does sustainability mean to you as an engineer working in Research and Development at Technoform?
In principle, plastic can only be sustainable if it can fully exploit its strengths. A plastic profile that fails after a short time in service is not sustainable. For me as an engineer, sustainability therefore begins with the question of whether plastic is fundamentally suitable for the desired application. If this is not the case, I recommend our customers switch to a more suitable material – and therefore a more sustainable one in their own individual case. Choosing the right material also plays a major role in terms of what happens to a plastic profile at the end of its service life. Speaking of recycling...
At Technoform, our guiding principle is consistent, universal recycling management. The aim is to recycle all our materials. If the specific application allows, I plan a residue-free recycling programme for the materials used, right from the start. Many of our customers now expressly request for their plastic profiles to be produced in this sustainable way. Materials that can be recycled don’t have to be bought new. This brings costs down without compromising on quality. But this has its limits. Thermoplastics cannot be recycled as many times as we want without losing some key material properties.
Dirk Moses, Head of Market Development at Technoform
How has the product life cycle of extruded plastic profiles changed in terms of its sustainability in recent years?
Sustainability is standard today when developing individual plastic profiles. Our customers set great store by working with materials that are environmentally friendly. That’s why our product life cycle planning does not end with a profile’s service life, but also takes into account the issue of recycling.
Ideally, a plastic product will follow the cradle-to-cradle principle and will be completely recycled at the end of its service life to become a new, similar product. In practice, however, this is rarely 100% possible since plastics lose certain properties – and therefore quality – required for the specific application when they are recycled. However, we try to recycle at least some of the processed material in our projects – always with the aim of delivering the best possible quality to our customers. So recycling is not an end in itself but must always centre on the product requirements.
What role do new materials, technologies and processes play in this regard?
A product’s design has a major impact on how long a plastic profile will last and how well it can be recycled at the end of its life. And choosing the right materials is crucial. The challenge is to balance a product’s technical requirements, its costs and its sustainability. That’s why we, as a service provider, don’t just implement specifications without checking them. Instead, we use our experience and expertise to support our customers in developing the best solution for them. We work with highly qualified suppliers to choose the right materials.
In addition to finding the right materials, technologies and processes also play a key role in sustainability. That’s why we work continually on optimising our process engineering and developing new approaches to make processable plastics that cannot be manufactured using standard processes. This includes injection moulding materials and materials with very high filler content, for example.
So if the requirements state that a plastic profile must have a extremely smooth surface or precise profile edges, we can use our special tools and processes to help ensure the product can ultimately be used for a very long time. If we were to choose to prioritise savings at this point, this might shorten the product’s service life, which would, in turn, negatively impact its sustainability. In addition, Technoform uses simultaneous engineering to quickly develop products ready for series production. Even tool manufacturing requires just a few test cycles. This helps us save on materials and avoid waste. So, you see, sustainability doesn’t work without the right materials, technologies and processes in place as part of the manufacturing process.
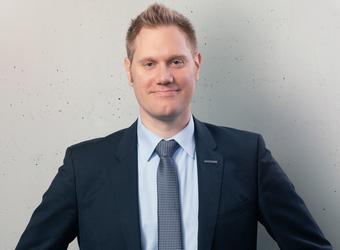
How do you think sustainability in plastics extrusion will progress in the coming years?
Sustainability is already not only something that is nice to have but is now standard in many industries. However, in many cases, sustainability is still limited to the narrow confines of discussions of cost. Only gradually are project managers beginning to understand that sustainable products also mean lower costs in the long term if at least some of the materials in their own product are recycled. This leads to a rethink in how we plan and budget for projects. The manufacturers of materials will also respond to this in the medium term, though they will be more concerned with renewable raw materials.
We will continue to develop plastics recycling, both in terms of processes and transparency in material life cycles. Ideally, every plastic product processed anywhere should be labelled and identified, even if it has already been processed or recycled. This would create greater transparency and security in terms of ensuring the quality of recycled materials for all parties involved – retailers, manufacturers and users.
Dirk, thank you so much for such an interesting interview!