The Art of Extrusion – Shaping, Designing, Optimizing
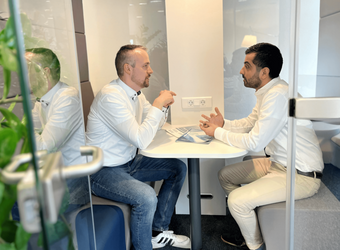
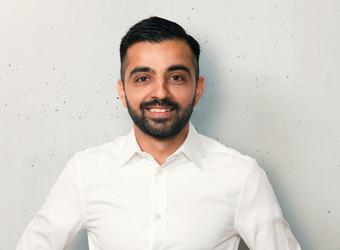
Konal, Technoform has been a leader in extrusion for over 50 years. What distinguishes your extrusion process?
Konal: As extrusion specialist for thermoplastics, we developed a specific continuous extrusion process. This method is more economical and efficient than processes like milling or injection molding. Thanks to our many years of extrusion experience, we achieve excellent surface quality and precision with a high filler content. The key is the optimal coordination of material, tool, and extrusion process.
What sets Technoform apart besides the technology?
Konal: We see ourselves not only as extrusion experts but also as development partners who advise customers early in product design. Our experts bring deep know-how in material processing and application development. The individual, in-house manufactured tool design is one of our special strengths.
What materials can you extrude?
Konal: Our focus is the extrusion of thermoplastic profiles made of polypropylene, polyamide, and PPS. These profiles are often reinforced with glass fibers and special additives such as UV protection, low thermal conductivity, or corrosion protection. Another advantage: Thermoplastic plastics are recyclable and sustainable.
How important is material selection for extrusion?
Konal: Material selection is crucial for successful extrusions. Materials are specifically chosen based on the later requirements of the end product. Exact specifications ensure consistent quality and efficient manufacturing parameters, which prevent defects during extrusion. Our R&D teams conduct intensive tests on new materials.
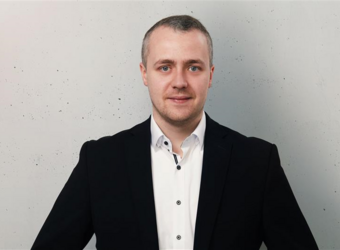
How long does a material change take?
Philipp: New materials undergo a long introduction and testing process. We face complex approval processes, for example in the construction industry and their regulations. Together with customers and suppliers, we also work specifically on integrating sustainable recycling materials (PIR and PCR) and to achieve the same quality results.
What do you value in material procurement for extrusion?
Philipp: High quality, reliability, and compliance with international standards (REACH, C2C) are our focus. We minimize risks through multiple proven suppliers and strive for long-term, social, and ecological partnerships.
The future of extrusion
Which technologies are changing the extrusion market?
Philipp: Future trends like sustainable construction increasingly determine development in the extrusion sector. We continuously optimize our extrusion process. Technologies like 3D printing offer potential for prototypes and toolmaking. New tool steels extend service life and open up new design possibilities for profiles. Smaller batch sizes are challenging but enable greater product variety. Sustainable raw materials and closed loops are becoming increasingly important.
What role do digital twins or simulations play for extruders?
Philipp: Digital twins enable more precise simulations through real-time data and support us in process optimizations. This allows materials to be used more efficiently and sustainably – a central contribution to the goal of a closed material cycle.