PPS: an alternative to PFAS?
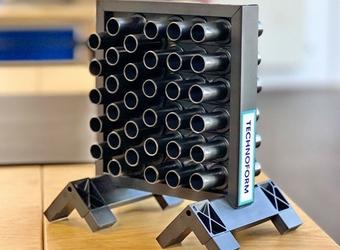
The search for materials that can replace fluoropolymers continues. In most cases, the property profiles of the substitute materials are not sufficient for the applications. But every now and then they succeed. Get to know the application.
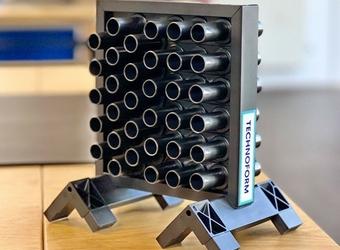
In response to increasing concerns regarding the environmental and health risks related to per- and polyfluoroalkyl substances (PFAS), the industry is increasingly looking for alternative materials that provide comparable performance without the associated disadvantages. Among the potential substitutes, polyphenylene sulphide (PPS) stands out as a promising candidate with a unique combination of properties that make it an appealing option for a large number of applications. What are the advantages of PPS and when can it replace fluoropolymers? What concerns regarding sustainability need to be taken into consideration?
Why PFAS needs to be regulated
The widespread use of PFAS in a great number of industrial applications, from extinguishing foam to non-stick coatings, has resulted in contamination of water sources and ecological systems all over the world. Because of the harmful effects of PFAS on human health and the environment, the European Chemicals Agency (ECHA) has initiated a process to either severely limit or to ban their use. As a result of these restrictions, the industry will need to reconsider its dependence on fluorinated materials and try to find alternatives.
Why fluoropolymers are so difficult to replace
Although it is inevitable that the use of PFAS will have to be avoided, finding suitable alternatives poses a complex challenge. Fluoropolymers are used in many different applications because of their outstanding properties. They provide a combination of chemical stability, heat resistance, water and oil repellent properties, low coefficients of friction and many other advantages.
Potential alternative materials ideally need to have similar benefits, and their toxicity, persistence and environmental impact also need to be taken into account. Furthermore, it is crucial for them to be compatible with existing manufacturing processes and supply chains, in order to enable a smooth transition. This makes selecting a material a highly complex process and means that the marginal constraints of any PFAS substitute need to be examined in detail. Because of these conditions, the selection of a substitute needs to be individually tailored to the specific application, as no other material can provide the same combination of positive properties as fluoropolymers.
Properties of the alternative material PPS
PPS represents a promising solution for replacing PFAS. It has a series of properties that make it a highly suitable material for a wide range of applications. These include:
- Thermal stability and performance: PPS has outstanding thermal stability and its melting point is above 280 °C. This inherent heat resistance makes PPS suitable as a material in high-temperature applications in sectors such as the automotive industry, aerospace and the electronics industry. The high-performance plastic retains its structural integrity and performance even under extreme conditions, making it reliable and long-lasting.
- Chemical resistance and durability: PPS offers outstanding resistance to a large number of chemicals, including acids, alkalis, solvents and other aggressive substances. Because of this property, it is suitable for applications in aggressive and highly corrosive environments such as chemical processing plants and power plants.
- Mechanical properties: As a high-performance plastic, PPS has good dimensional stability, stiffness and strength. Depending on the application, these properties can be modified with various filler materials such as glass fibre.
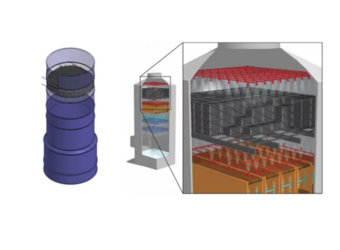
Another application for PPS is a frame structure that was created as part of a development project for the flue gas industry. The profiles of the frame are manufactured from fibre-reinforced PPS and are used in flue gas scrubbers in coal-fired power plants. The frames are used as a fixture for filters that remove mercury and sulphur dioxide from the power plant’s exhaust gases. In this application, the PPS profiles are exposed to both elevated temperatures and highly corrosive chemicals (HCl, H2SO4, HF, HNO3) that are deposited on the filters.
This PPS solution provides better durability and better mechanical properties than frames made from expensive special alloys while reducing costs.
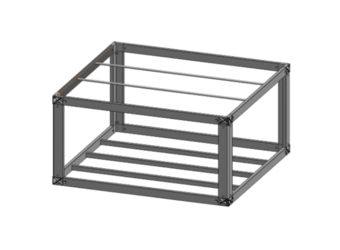
Case-by-case decisions necessary
With its exceptional thermal stability, chemical resistance and environmental advantages, polyphenylene sulphide is a sustainable and environmentally sound alternative to PFAS. Nevertheless, individual material testing needs to be performed for every potential application, as PPS cannot be used as a substitute in all cases. It provides a valid solution for a number of challenges that will be posed by the coming bans on PFAS. Using PPS will enable the industry to meet regulatory requirements, minimise risks and move towards a more sustainable future.
This article was published by plastverarbeiter.de: PPS: Eine Alternative zu PFAS?