Plastic profiles in electrical engineering: Which material is the right one?
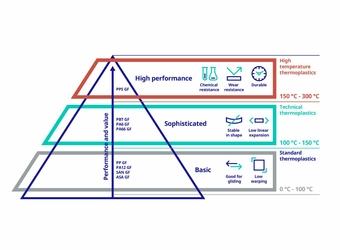
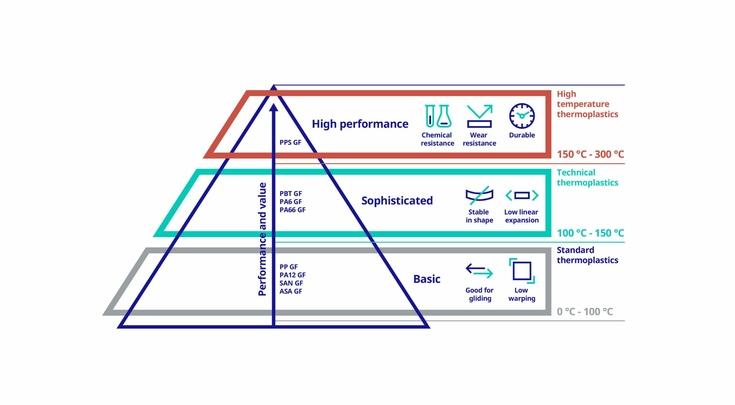
Plastic components for electrical engineering
Plastic components for electrical engineering must fulfil high requirements. Choosing the right material is therefore crucial to success. We give you a quick overview of engineering plastics and their properties that play a role in electrical engineering.
Increasingly safer, more stable, thinner and lighter
The complexity of electronic applications is growing and with it the demands on the plastic components used. The safety-related approval hurdles in particular are high. This is particularly true in highly sensitive areas. Here, for example, plastics can significantly reduce the risk of fire and explosion.
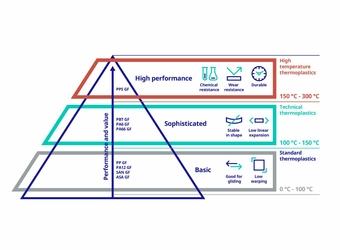
The following overview shows which plastics are suitable for which temperatures. A distinction is made between three groups:
Standard plastics, technical plastics and high-temperature plastics.
The first group is classically used in free extrusion and is heat-stable up to 100 degrees.
Engineering plastics, such as the frequently used polyamide, are stable up to 150 degrees.
The third group is still dimensionally stable even at temperatures of up to 300 degrees and is therefore suitable even for the highest requirements, for example in space technology.
In order to fulfil the high fire protection requirements in electrical engineering, all components must be self-extinguishing in accordance with UL94. This high flame resistance is usually achieved by adding additives.
High demands: stability
In addition, electrotechnical components made of plastic must be increasingly stable in order to fulfil the requirements in practice. High rigidity and impact strength are required above all if the component is to replace metals. The purity of the plastics plays an important role here. The purer the material, the more reliable the component made from it.
A particular challenge arises when components have to fulfil high safety requirements while keeping material thickness and weight as low as possible. This is the case with electric motors, for example. In order to ensure both, in practice a plastic that naturally has favourable properties is optimised for the specific application using fillers that increase its rigidity, for example.
It's all in the mix: How plastics are optimised for your application
An optimal plastic is like a good cuvée wine: the right blend leads to the optimal result. Fillers and additives can be added to change or supplement certain material properties depending on the requirements.
Here are some examples of fillers and additives in engineering plastics:
- Fillers are fibres and/or particles that change the mechanical, electrical or thermal properties (e.g. strength, toughness, conductivity).
- Additives can be used for optical or chemical adjustments (e.g. colour, better processing).
- UV light stabilisers (UV absorbers, quenchers) prevent colour changes or a reduction in mechanical properties due to UV light.
- Flame retardants (halogenated, phosphorus-containing, inorganic) serve to prevent or delay the spread of fire.
- Processing aids (flow aids, nucleating agents, lubricants) ensure faster and more cost-effective processing.
- Especially for use in electrical engineering, there is a wide range of ready-made plastic products that fulfil the most diverse requirements. As experts in plastics processing, we support you in selecting the right product for you.
- Plastics for high-precision processing
Our goal at Technoform is to always find the best possible solution for our customers' requirements. To do this, we use a specially developed process for "high-end extrusion", which enables particularly smooth surfaces, sharp contours and the lowest tolerances in production.
What doesn't fit is made to fit
There are plastics with suitable properties for every requirement for electrotechnical components. Where properties are missing or disruptive, the material can be customised using fillers and additives. We will be happy to advise you on the selection of the right materials.