泰诺风协助西雅图布利特中心成为世界上最环保的商业建筑
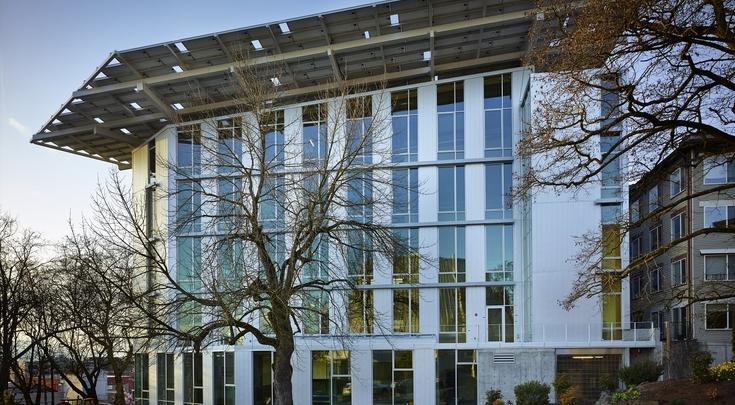
Technoform is helping the Bullitt Center achieve its net-zero energy goals and to become the first commercial office building to earn Living Building Challenge certification. Located in Seattle’s Capitol Hill neighborhood, the $18.5 million project opened on Earth Day, April 22, 2013 and intends to have the building last until 2263.
Pursuing Living Building Challenge certification
“The greenest commercial building in the world,” boasts the Bullitt Center’s website. Through the International Living Future Institute, Living Building Challenge (LBC) certification poses the most rigorous performance standards across the globe. Validation includes submitting 12 months of post-occupancy data to demonstrate annual operations for net-zero energy and water, plus a zero carbon footprint. Along with performance, LBC also requires a building to be useful, healthy and beautiful.
The six-story, 52,000-square-foot, Class A office building’s unusually tall 14-foot floor-to-floor heights are matched with equally impressive floor-to-ceiling operable window systems. These spacious, daylit areas provide expansive views of the downtown skyline and connect the building’s occupants with their surrounding environment.
Named for its owner, the Bullitt Foundation strives to safeguard the natural environment through promotion of responsible human activities and sustainable communities in the Pacific Northwest. Point32 served as the developer for the Foundation’s new headquarters. Sharing the Bullitt Foundation’s vision, Point32 selected Miller Hull Partnership as the architect and Schuchart Construction as the general contractor.
“The attention-getting elements of the Bullitt Center -- 100% onsite renewable energy, water and waste management, as well as a safe, naturally day-lit and ventilated work environment built to last 250 years -- follow from an equally exciting integrated design process that enabled us to move beyond the traditionally linear design, engineering and construction process to orchestrate a diverse team targeting the seemingly impossible together, right from the start,” said Craig Curtis, design partner with The Miller Hull Partnership.
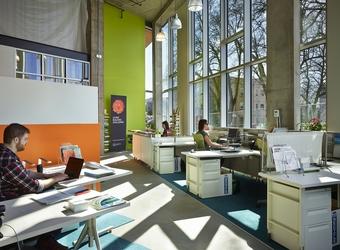
Optimized for net-zero energy goals
Early in the project’s development, Washington-based glazing contractor Goldfinch Brothers involved glass fabricator Northwestern Industries to assist with performance calculations, color selection and other architectural support. The duo had teamed with Technoform on previous projects. For the Bullitt Center, Northwestern Industries fabricated the glazing system using TGI®-Spacer for Schüco curtainwall and operable window systems with PPG Solarban® 60.
“Everything went great in meeting the performance requirements and fabricating the dual- and triple-glazed units. Because of the tight job site, we were fabricating and shipping what was needed week-by-week,” says Brian Brunette, Northwestern Industries’ sales manager. “Technoform does a good job with their support and follow-up. They regularly checked in to make sure everything was going well and that we had the materials that we needed.”
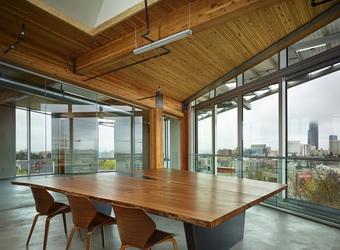
Bullitt Center’s operable windows capitalize on natural ventilation coupled with a heat-recovery system and weather-responsive shading system. Prior to fabrication and construction, computer simulations modeled daylight illumination for different window configurations and ceiling heights to optimize energy efficiency.
Further contributing to building’s energy goals and the occupants’ comfort, the window system’s Technoform spacer not only maximizes thermal performance and condensation resistance, but also enhances acoustic performance for quiet interiors. Schüco’s curtainwall’s insulating glass units are triple-pane and weigh up to 468 pounds. The majority of these units are two inches thick and comprised of a Technoform spacer plus two lites of glass with low-e coating on the second and fifth surfaces. The spacers vary in size from 1/2-inch to 5/8-inch (1.27 to 1.59 cm). This composition attains a U-factor of 0.17 BTU/hr.ft2.ºF and condensation cating of 86 can be achieved.
“We were able to get the best U-factor for the architect using Technoform’s spacer,” says Javier Bonilla, project manager with Goldfinch Brothers. “It went well with the glazing and was a fun project.”
Javier Bonilla, project manager with Goldfinch Brothers
Technoform's patented spacer design combines the benefits of high-performance polymers and thin stainless steel, setting the performance standard for insulating glass products. TGI-Spacers were one of thousands of building materials in the Bullitt Center that were vetted thoroughly for compliance with the LBC “Red List” of 14 potentially toxic substances. Many of these substances, such as PVC and formaldehyde, are common in building materials.
“It is important that we look forward, look ahead, and find products that are effective and affordable,” says Greg Goldfinch, president of Goldfinch Brothers. To him, the Bullitt Center exemplifies the future of sustainable commercial construction. “It really is going to be a showcase for a Living Building Challenge, a net-zero building, and to be a part of that is pretty special.”
“It’s really incredible,” praises Amanda Sturgeon of the International Living Future Institute. “It’s proof at a size and in a location where people can interact and be aware of it and be part of the process.”
Craig Curtis, FAIA, design partner at Miller Hull, continues, “In considering first and foremost how to design a building with essentially no environmental footprint, it was energizing to identify imaginative and elegant ways to beautifully express the building’s core performance functions through design strategies using a mix of existing and new technologies, systems, and materials. While in one sense we had to do more with less, we happily found that designing to high-performance targets actually opened up numerous formal design opportunities.”
From Architectural Record to The New York Times to Wired, dozens of architectural, sustainability and business media outlets have complimented the Bullitt Center’s design. The project also has been honored by the American Institute of Architects’ Seattle chapter’s What Makes It Green Awards, Architizer’s A+ Awards, Eco-Structure magazine’s Evergreen Awards, the Forest Stewardship Council’s Design & Build with FSC Award, Seattle Business magazine’s Green Washington Awards and others.
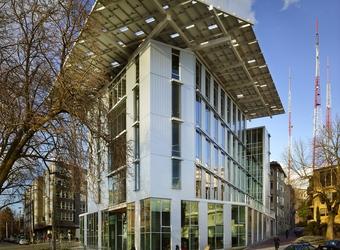
Seeking more than trophies, Denis Hayes, president of the Bullitt Foundation, says, “We’re just trying to make it a building where doing the right thing, the healthy thing, the environmentally sound thing, is also the convenient thing.” He concludes, “Our whole purpose is to be an instrument of change. And to use this building not just to influence developers and architects, but… all of the people who are involved in making these kinds of decisions.”
- Bullitt Center, 1501 East Madison St., Suite 600, Seattle, WA 98122
- Owner: Bullitt Foundation; Seattle
- Architect: Miller Hull Partnership, LLP; Seattle
- Developer: Point32, LLC; Seattle
- General contractor: Schuchart Construction; Seattle
- Glazing contractor: Goldfinch Brothers, Inc.; Everett, WA
- Glazing systems – manufacturer: Schüco USA L.P.; Newington, CT
- Glazing systems – glass fabricator: Northwestern Industries, Inc.; Seattle
- Glazing systems – glass supplier: PPG Industries; Pittsburgh, PA
- Glazing systems – thermal spacer systems manufacturer: Technoform; Twinsburg, OH